Machine and Lubrication: Ensuring Smooth Operations
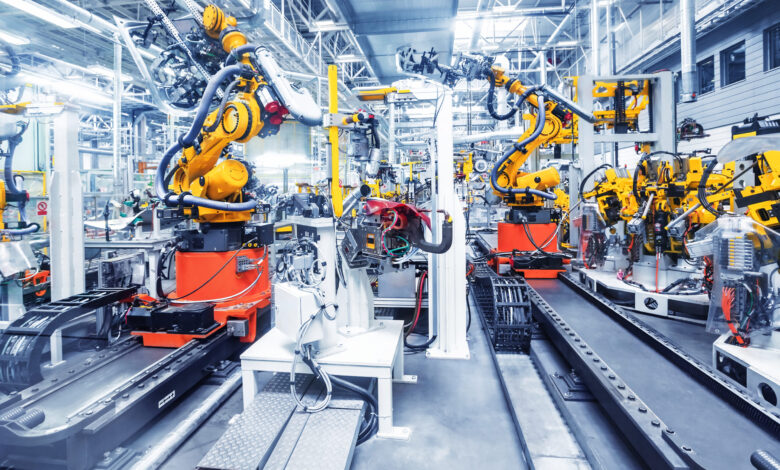
Introduction to Machine Lubrication
https://isohitech.com/ Lubrication plays a critical role in the performance and longevity of machinery across various industries. From heavy manufacturing equipment to delicate precision instruments, proper lubrication is essential for ensuring smooth operations and minimizing wear and tear.
Importance of Lubrication in Machinery
Lubrication serves multiple purposes in machinery. Firstly, it reduces friction between moving parts, thereby minimizing wear and extending the lifespan of components. Secondly, it helps dissipate heat generated by friction, preventing overheating and potential damage. Additionally, lubricants act as barriers against moisture and contaminants, reducing the risk of corrosion and rust formation.
Types of Lubricants
There are several types of lubricants available, each suited to specific applications and operating conditions. Oil-based lubricants, such as mineral oils and synthetic oils, are commonly used for their ability to flow and provide continuous lubrication. Grease lubricants, comprising oil suspended in a thickener, offer better adhesion and are ideal for components subjected to heavy loads or shock. Dry lubricants, such as graphite and molybdenum disulfide, provide lubrication in environments where liquid lubricants are impractical or undesirable.
Factors Affecting Lubricant Selection
https://mikeshoppingroom.com/ The choice of lubricant depends on various factors, including operating conditions, temperature, speed, and load. For instance, high-temperature applications may require lubricants with high thermal stability, while low-speed, high-load applications may necessitate greases with extreme pressure additives.
Common Lubrication Techniques
Lubrication can be performed manually by applying lubricants directly to components or through automated systems. Automatic lubrication systems, such as centralized lubrication units or progressive lubricators, ensure consistent and precise application of lubricants, reducing the risk of over or under-lubrication. Circulating oil systems are employed in large machinery with complex lubrication requirements, where oil is continuously circulated through the system to provide lubrication and cooling.
Proper Lubrication Maintenance
Regular maintenance is crucial for effective lubrication management. This includes periodic inspections to check for leaks, contamination, or signs of inadequate lubrication. Lubricant analysis, through techniques like oil sampling and spectroscopy, helps monitor the condition of lubricants and detect any abnormalities. Establishing a comprehensive lubrication schedule ensures that machinery receives timely lubrication, minimizing the risk of breakdowns and optimizing performance.
Consequences of Poor Lubrication
Inadequate lubrication can have detrimental effects on machinery, leading to increased friction, wear, and premature failure. Over time, frictional forces can cause components to seize or wear out, resulting in costly repairs or replacements. Additionally, overheating due to insufficient lubrication can damage seals, bearings, and other critical components, leading to unplanned downtime and production losses.
Best Practices for Effective Lubrication
To ensure optimal lubrication performance, it’s essential to adhere to best practices recommended by equipment manufacturers and industry standards. This includes using the right type and grade of lubricant specified for the application, applying the correct amount to achieve proper lubrication film thickness, and following prescribed maintenance intervals. Proper storage and handling of lubricants, including protection against contamination and degradation, are also essential for maintaining lubricant quality and performance.
Case Studies
Several industries have successfully implemented lubrication strategies to improve efficiency, reliability, and safety. Case studies highlighting these successes demonstrate the tangible benefits of proactive lubrication management, including reduced maintenance costs, extended equipment life, and enhanced productivity.
Future Trends in Machine Lubrication
https://incomepultrusion.com/pultrusion-machine/ Advancements in lubricant technology and maintenance practices are driving future trends in machine lubrication. Predictive maintenance techniques, enabled by sensor technology and IoT connectivity, allow for real-time monitoring of equipment condition and performance, enabling proactive maintenance interventions and minimizing unplanned downtime. Additionally, developments in eco-friendly lubricants and recycling initiatives aim to minimize the environmental impact of lubrication practices while ensuring sustainable operations.
Environmental Impact of Lubricants
As environmental awareness grows, there is increasing emphasis on the use of biodegradable lubricants and environmentally friendly lubrication practices. Biodegradable lubricants, derived from renewable sources or synthetic esters, offer comparable performance to conventional lubricants while minimizing ecological impact. Proper disposal and recycling of used lubricants are essential to prevent contamination of soil and water sources, emphasizing the importance of responsible lubricant management practices.
Cost-Effectiveness of Proper Lubrication
While proper lubrication management entails initial investment and ongoing maintenance costs, the long-term benefits far outweigh the expenses. By reducing friction, wear, and downtime, effective lubrication strategies contribute to significant cost savings over the equipment’s lifespan. Moreover, proactive maintenance practices, such as lubricant analysis and condition monitoring, help identify potential issues early, preventing catastrophic failures and costly repairs.
Challenges and Solutions in Lubrication
Despite advancements in lubrication technology, challenges persist, particularly in harsh operating environments or specialized applications. Extreme temperatures, high loads, and corrosive atmospheres can pose significant challenges to lubrication effectiveness and longevity. However, innovative solutions, such as advanced lubricant formulations, specialty additives, and tailored maintenance programs, help mitigate these challenges and ensure reliable performance even in the most demanding conditions.
Regulatory Compliance and Standards
Compliance with industry standards and regulations is essential for ensuring safe and efficient lubrication practices. Organizations such as the International Organization for Standardization (ISO) provide guidelines and specifications for lubricant selection, handling, and storage. Additionally, adherence to safety regulations and best practices, including proper labeling, handling procedures, and personnel training, minimizes the risk of accidents and environmental contamination associated with lubricant use.
Conclusion
In conclusion, effective lubrication management is essential for maintaining the performance, reliability, and longevity of machinery across diverse industries. By minimizing friction, dissipating heat, and protecting against wear and corrosion, proper lubrication ensures smooth operations and prevents costly breakdowns. Adopting best practices, leveraging technological advancements, and prioritizing environmental sustainability are key to optimizing lubrication performance and maximizing equipment lifespan.
Unique FAQs:
1. Why is lubrication important for machinery? Proper lubrication reduces friction, minimizes wear, dissipates heat, and protects against corrosion, ensuring smooth operations and prolonging equipment lifespan.
2. How often should machinery be lubricated? Lubrication frequency depends on factors such as operating conditions, equipment type, and manufacturer recommendations. Regular inspections and maintenance schedules help determine optimal lubrication intervals.
3. What are the consequences of over-lubrication? Over-lubrication can lead to increased operating temperatures, leakage, and waste, potentially causing damage to seals, bearings, and other components. It can also attract contaminants, compromising lubricant effectiveness.
4. Are there environmentally friendly lubrication options available? Yes, biodegradable lubricants made from renewable sources or synthetic esters offer environmentally friendly alternatives to conventional lubricants, reducing ecological impact without sacrificing performance.
5. How can predictive maintenance improve lubrication practices? Predictive maintenance techniques, enabled by IoT technology and data analytics, allow for real-time monitoring of equipment condition and performance, enabling proactive lubrication interventions and minimizing downtime.